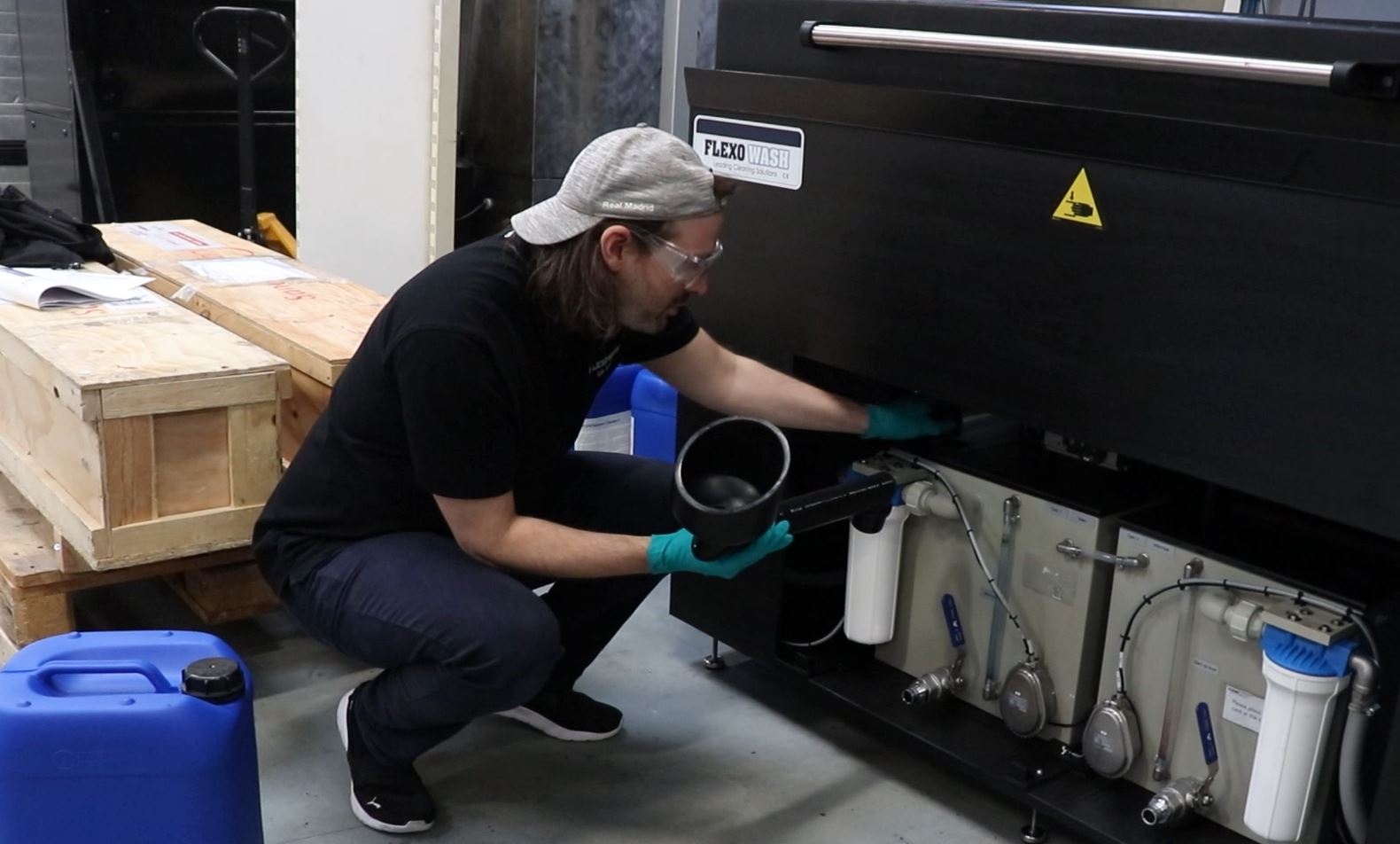
When you have to install one of our PK ECO parts washing systems, you will find that it is quite...
The fully automatic washing units are designed for easy handling of press parts. It is possible to wash doctor blade chambers, ink trays, ink sumps and other removable press parts used with all types of inks, varnishes etc. The units can be equipped with a trolley, which makes the handling even easier.
The Parts Washers from Flexo Wash have a Wash & Rinse system with two separate tanks which offers an automatic two-stage cleaning process, where the first stage is for cleaning and the second stage is for rinsing.
The parts are cleaned by various high-pressure nozzles, spraying cleaning and rinse liquid from below and above.
All units can be customized according to each customer’s specific needs. They are made with a moving nozzle arm, which ensures a more dynamic liquid flow, a higher pressure and thus an improved wash result.
Different needs require different techniques. Therefore, the Flexo Wash EasyLoad & FrontLoad parts washers can all be built to clean with solvents, alkaline liquids or eco-friendly cleaning liquids and distillable eco-friendly liquids.
Factors like ink types, thickness of ink layers, installation space etc. determines which kind of PK unit you should choose. Below you will find brief info of each type of cleaning method.
This standard unit is designed to clean with eco-friendly liquids and distillable eco-friendly liquids.
The machine is recommended when non-flammable liquids are used in the machine.
These units are made either with a microprocessor control system (EasyLoad-series) or PLC control system (FrontLoad-series)
Cleans both water- and solvent-based inks, varnishes & lacquers in one single machine.
Alkaline liquids are the most efficient way to remove 2K and other difficult ink residues.
The units do not need special space for installation, like e.g. an ATEX room. It allows you to solve even difficult cleaning jobs without installing a more space consuming ATEX solution.
The electric ATEX washing unit is the latest generation of parts washers for intensive use and high demand of removal thick ink-layers.
The machine will be built to work with solvents and will be made EEX-proof according to the ATEX standard.
The units are made with a PLC control system and electrical pumps. We can also supply a ATEX Pneumatic version of these units.
When cleaning with solvent, special precautions must be taken in order to completely neutralize the risk of explosion or fire in the immediate area. Flexo Wash takes these precautions by delivering washing equipment according to the ATEX directive 2014/34/EU intended for use in potentially explosive atmospheres.
Flexo Wash collaborates with notified bodies for approval of the equipment, ensuring that each unit is safe being EEX-proof according to the ATEX standard and certified by ExVeritas.
ZONE 0 = CATEGORY I:
Explosive atmosphere is continuously present for long periods. Inside the washing unit and tanks the unit will have ATEX zone 0
ZONE 1 = CATEGORY II:
Between 10 and 100 hours of explosive atmosphere per year. Around the unit will be ATEX zone 1.
ZONE 2 = CATEGORY III:
Less than 10 hours of explosive atmosphere per year. Zone 2 is often referred to as the remotely hazardous area.
We supply parts washing equipment in all sizes for all segments of the flexographic and gravure industry. The Flexo Wash Parts Washers comes in many different models which each can be modified by combining the standard unit with one or more of the various options.
We have been leading experts in parts washing for 30 years and our large portfolio of units and options reflects the flexibility needed to meet all needs of the fleoxgraphic and gravure industries.
With the EasyLoad/ SideLoad units you will get a very effective and cost-efficient parts washer for various wide web press parts. The machines are controlled by a microprocessor, where it is easy to set the different programmes such as wash time.
The standard unit comes with one large trolley which makes it easy to move the parts directly from the printing press to the grid.
The grid is then easily slid into the PK EasyLoad/ SideLoad from the trolley, thus eliminating handling to a minimum.
With the FrontLoad units you will get highly intensive 360° cleaning by nozzles from four sides of the parts. The machines are controlled by a PLC control system for a user-friendly and easy use of the machine.
The standard unit comes with two trolleys which makes it easy to move the parts directly from the printing press to the grid.
The grid is then easily slid into the PK FrontLoad from the trolley, thus eliminating handling to a minimum.
When you have to install one of our PK ECO parts washing systems, you will find that it is quite...
Written by Lasse Barbier SøndergaardWhen you are going to install one of our machines, you will find out that it is very simple. But...
Written by Lasse Barbier SøndergaardThe Trolley Wash machine gives you a very effective and cost-efficient parts washer for various...
Written by Anders KristoffersenThe unit has made a terrific difference to the cleaning regime and has achieved great results!
Click the buttons for contact regarding service or liquids - else please fill in the form below and let us know how we can help you.
Please fill in the form below and let us know how we can help you.
Please fill in the form below and let us know how we can help you.