What if your press operators could focus on what they do best?
Topics
01. Having trouble cleaning your parts? 02. Is your cleaning liquid tailored to your inks? 03. Did you know a cleaning system could save you money? 04. Are you maximizing the lifespan of your screens? 05. Looking for an easier way to clean plates? 06. Expand you knowledge - Resources 07. Download our guide
Having trouble cleaning your parts?
In the label printing industry, maintaining high-quality print results and minimizing downtime depend on the condition of press parts. Anilox, ink trays, doctor blades, ink pumps, and other key parts require proper care to extend their lifespan and ensure consistent performance. With the right maintenance strategy and cleaning solutions, you can reduce wear and tear while keeping your equipment in optimal condition.
Dried ink, coatings, and adhesives can build up on essential components, leading to print defects and premature wear. Flexo Wash’s automated cleaning systems ensure thorough and consistent cleaning of anilox rolls, ink trays, and other parts without causing damage. Whether using our liquid-based cleaning technology or laser cleaning solutions, Flexo Wash helps maintain peak performance while reducing manual labor.
Whether you're running UV, solvent, or water-based inks, our fully automatic parts washing systems handle the toughest residues to keep your presses performing at their best.
Our solutions are designed to meet the unique needs of the label industry, ensuring effective cleaning of:
✔ Ink trays, chambers, and doctor blades
✔ Buckets and mixing tools
Read what our customers think about their parts washer installations of parts washing in the label industry or read our blog about how we can custom build parts washers for your needs.
Is your cleaning liquid tailored to your inks?
Is your cleaning liquid tailored to your inks?
In label printing, maintaining clean press parts is important for achieving consistent print quality, minimizing downtime, and prolonging the lifespan of key components.
Can you recognize yourself as the label printer that uses both water-based and UV-based inks? Then we have a cleaning solution for you! Our cleaning liquids are tailor-made for your ink types. Let us help guide you to how you can make money by having an automated cleaning system.
Did you know a cleaning system could save you money?
Some label printers will probably say that cleaning UV inks is easy; they say that you just take a cloth and then it is clean. But other printers in the label industry will say that using UV inks can lead to a mess if the used items are not handled and cleaned properly. If you get UV ink on your fingers or your shoes, it is everywhere. So why not choose a cleaning system that saves you time on cleaning and still cleans your parts?
Many label printers face problems when they clean parts, especially doctor blade chambers, where you can easily cut yourself on the blade. No one wants their employees to get injured. Flexo Wash offers parts washers customized for your parts so you can avoid cuts in your operation and still have clean parts. By implementing a comprehensive cleaning solution, label printers can ensure consistent quality across all production lines. A tailored cleaning package helps optimize workflows, reduce manual labor, and eliminate inefficiencies, allowing operators to focus on production rather than cleaning.
Companies like Desmedt have already seen the benefits of investing in a complete Flexo Wash cleaning package, which has enabled them to enhance print quality and streamline operations. With the right cleaning technology, label printers can achieve higher efficiency, reduce press downtime, and maintain the highest production standards.
Desmedts Flexo Wash package:
- PK 200 WR TrolleyLoad Parts Washer, with a small trolley for UV Ink,
- PK ECO Maxi WR Parts Washer for water-based ink.
- FW 993 XL Anilox Roll Cleaner that handles up to nine rolls per wash,
- PK 92 Screen Washer
- PW 82 WR Plate Washer.
- PK Filtration Unit that can be used for both the PK 200 and the PW 82 machines.
Would you like to know more about how a complete cleaning package can benefit your print operation? Contact us to discuss your specific needs.
Are you maximizing the lifespan of your screens?
Do you find it difficult to clean screens manually? Many label printers don't reuse their screens. The screens can be very fragile and therefore if you clean them manually they can easily be damaged.
Screens can be cleaned in a machine and reused afterward. And who doesn't want to save money and think sustainable? Can you identify with this problem? And would you like to change this problem in your production? Then Flexo Wash can help you.
Looking for an easier way to clean plates?
Discovering a print error while the press is running can be both frustrating and costly. While print defects can emerge from various factors, one common cause is a damaged or improperly cleaned plate. Manual cleaning, if done incorrectly, can compromise the plate’s integrity, leading to print quality issues and unnecessary downtime. Cleaning printing plates is more complex than it may seem. Achieving even pressure across the entire plate during manual cleaning is challenging, increasing the risk of damage. Replacing plates is expensive, but the true cost lies in lost production time when the press is not running.
Considerations for your operation
-
How many hours per year is the press not running due to damaged plates?
-
How much money do you spend on plates that are damaged due to manual cleaning?
Even if your facility produces plates in-house, production halts while new plates are made. The cost escalates further if a job must be restarted due to a minor defect. Read our blog: The domino effect of damaged plates to read more about the effect of having damaged plates in your production.
Choosing the right plate cleaning solution
When selecting a plate washer, it is essential to consider not only cleaning effectiveness but also operational efficiency and labor requirements.
Would you prefer a system where:
-
Plates must be manually fed into the machine?
-
Plates require precise placement on an adhesive surface to prevent liquid exposure on the reverse side?
-
A solution where plates can be placed in front of the machine, allowing for automated cleaning with minimal operator involvement?
Advantages of automated plate cleaning
✔ Consistent and thorough cleaning
✔ Reduced manual labor requirements
✔ Effective removal of all ink types
✔ Extended plate lifespan and enhanced print quality
Investing in an automated plate cleaning system ensures efficiency, minimizes downtime, and protects the quality of your print production.
Expand you knowledge - Resources
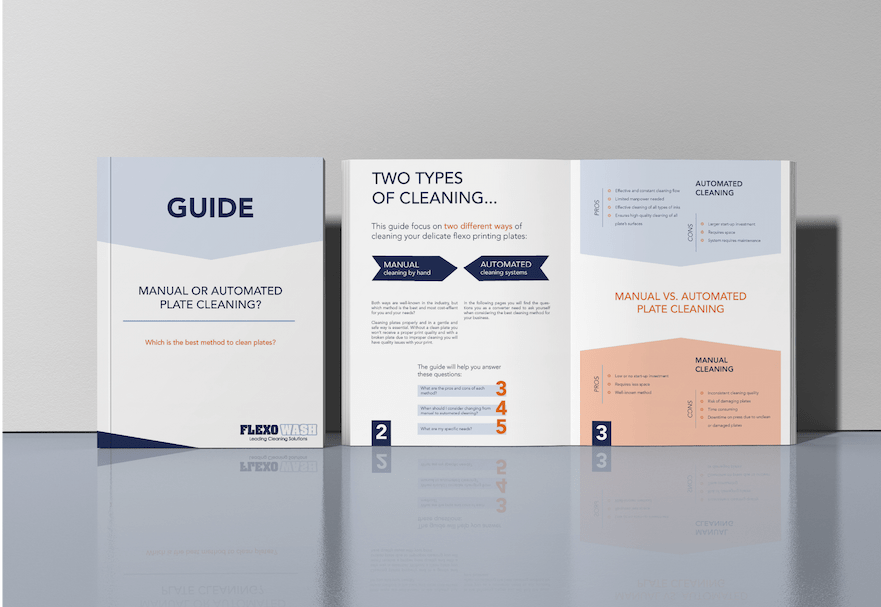
Download our guide
See how you can reduce downtime, increase print quality, cut costs, and get a better work environment. In short, find out how to stay ahead of your competitors.